How Our Virtual Packaging Manager Can Transform Your Ordering Experience.
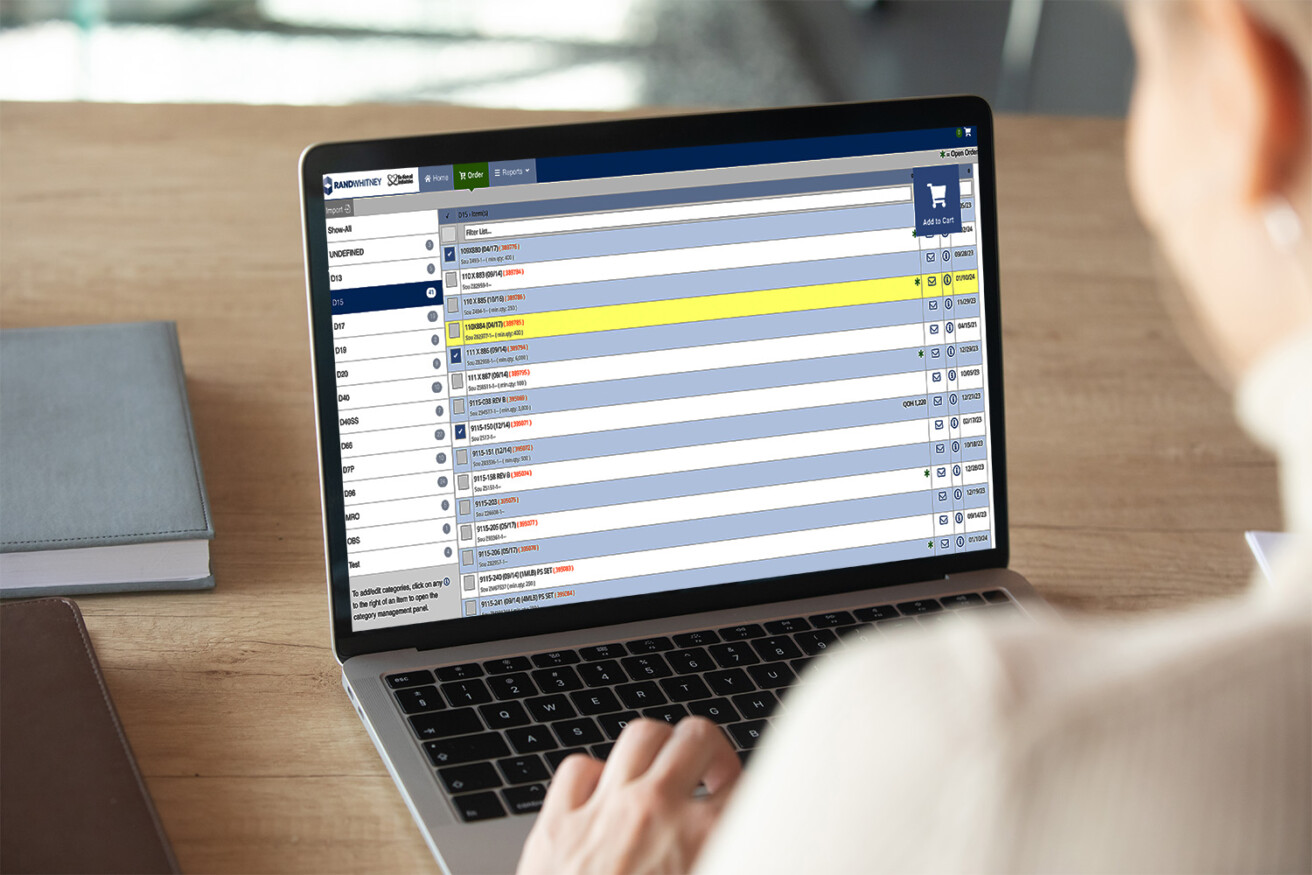
Challenge
For customers that sell a large number of unique products, the amount of packaging SKUs can add up quickly. One of our customers had over 200 items that were used in different silos of their manufacturing process. They placed over 20 orders each day through their customer service representative. It became hectic for their team to track inventory levels and stay on top of purchase orders as their business continued to grow.
Solution
We introduced a solution that utilized our internally built virtual packaging management system to make ordering and inventory management easier than ever. In each section of their manufacturing plant, we gave a tablet and purchasing power to a key facilitator. Each facilitator was in charge of the items that they use and now place orders on the tablet with a touch of a button. Inventory levels and all ordering information is tracked in our system.
Results
By giving purchasing power to the day-to-day users, inventory tracking and reordering became much easier. The person using the packaging is the first person to know when levels get low and now they have the ability to replenish live, right on their tablet. This turned 200+ items and 20+ daily orders into a much more efficient and manageable system. An added benefit of utilizing our virtual packaging management system is that usage data, order history, and analysis tools track your packaging spend in real time, giving you actionable metrics that managers can use to keep an eye on the bigger picture with complete visibility into all of your different business silos.